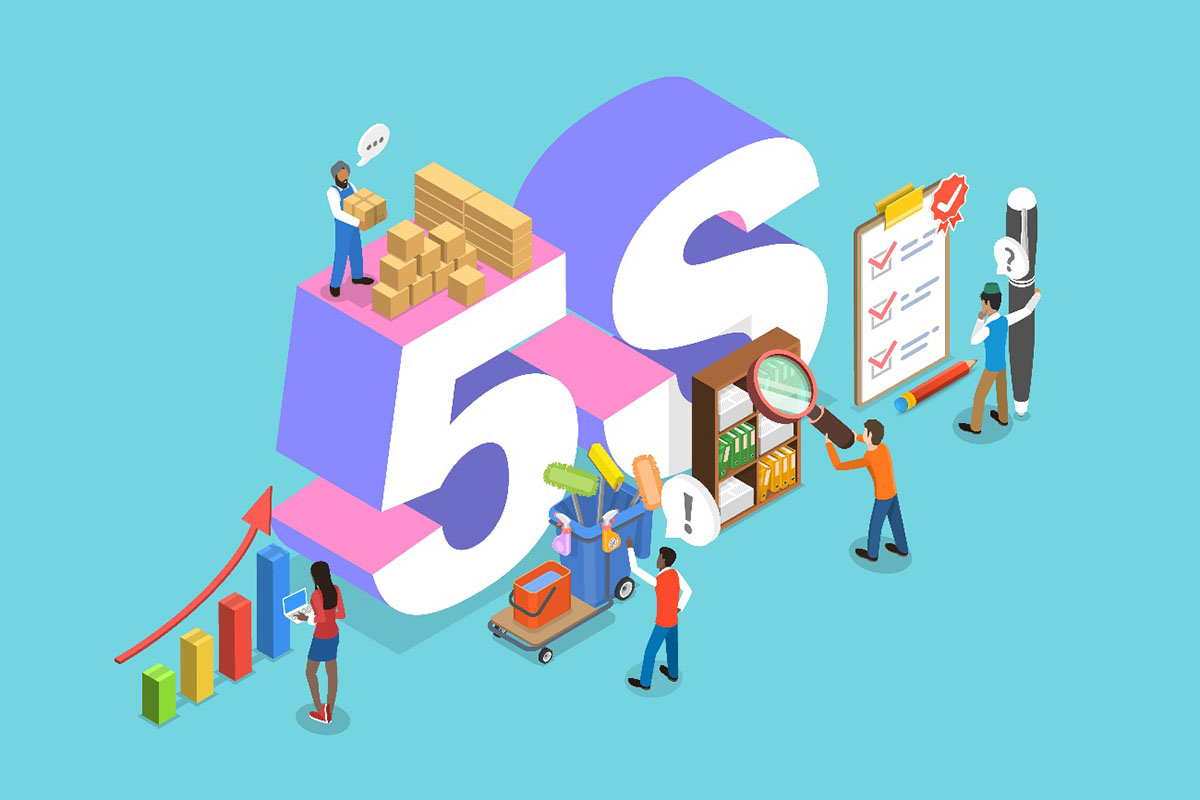
5Sとは、「整理、整頓、清掃、清潔、躾」の5つの要素で、職場の効率化と安全性向上を目指す活動のことを指します。本記事では、5Sの基本概念から実践方法、さらに5Sを取り入れた企業の成功事例をご紹介します。
2025/01/30 公開
目次
5Sとは?
5Sとは、職場の効率化と安全性向上を目指すための、5つの要素(①整理、②整頓、③清掃、④清潔、⑤躾)を指します。
職場環境の改善や生産性向上に取り組む中堅社員や管理職の皆様にとって、5S活動は避けて通れない重要なステップです。しかし、実際に取り組んでみると、活動が定着しなかったり停滞したり、効果が見えにくくなったりすることも少なくありません。そんな時にこそ、他社の成功事例を参考にし、新たな視点を得ることが必要です。
本記事では、5Sの基本概念から実践方法、さらに成功事例を通じて、5Sを実施するためのヒントを提供します。あなたの職場でも5Sを活用し、より良い環境を築いていきましょう。
今すぐできる職場環境の改善が、5Sです!
職場環境の改善を図るために、今すぐ取り組める方法として「5S」があります。5Sは、日本の製造業界で生まれ、世界中で広く採用されている職場改善の手法です。歴史を振り返ると、1950年代に日本の工場で生産性を向上させるために開発され、その後、品質管理の一環として広がりました。
◾️ 5つの要素:整理、整頓、清掃、清潔、躾
5S活動は、整理、整頓、清掃、清潔、躾の5つの要素から構成されています。
- 「整理」:必要なものと不要なものを区別し、必要なものだけを残すこと
- 「整頓」:必要なもの使いやすいように配置し、効率的に作業を進めるための工夫をすること
- 「清掃」:日常的に職場をきれいに保つこと(機械や設備の点検も含む)
- 「清潔」:職場の整理・整頓・清掃が行き届いた状態にすること
- 「躾」:習慣化の意味。これらの活動を習慣化し、持続可能な職場環境を築くこと
◾️ 5Sの導入による職場環境改善の効果
5Sを導入することにより、職場環境は大きく改善されます。まず、整理と整頓によって物事に優先順位がつき、快適な作業スペースが確保されます。精神的にも物理的にも余裕をもって作業ができるようになります。これによって作業効率が向上し、無駄な時間を削減できます。
また、業務の生産性が高まれば、業務負担が軽減されコミュニケーションコストも抑えられるため、管理者も従業員もストレスが軽減されます。
清掃と清潔を徹底することは、職場の安全性の向上につながります。整理・整頓・清掃が行き届いた清潔な職場では従業員の事故や怪我のリスクを減少させることができます。
躾による習慣化は、これらの改善を持続可能にし、長期的な職場環境の向上に寄与します。
5S活動を通じて、従業員の意識改革が進み、職場全体のモチベーションが向上することも期待できます。
◾️ 「4S」と「5S」の違いは?それぞれのメリットと注意点
「4S」と「5S」は、どちらも職場改善の手法として知られていますが、5Sには「しつけ」が加わる点が特徴です。4Sは整理、整頓、清掃、清潔の4つのステップを指し、職場の効率性と安全性を向上させる取り組みです。一方、5Sは4Sに「しつけ」を加え、習慣化を促進します。
4Sの段階では、基本的な整理整頓が主な目的ですが、5Sではさらに従業員の意識改革を目指します。
5Sの実践方法とステップ
5S活動は、整理、整頓、清掃、清潔、躾の5つの要素から構成されています。
職場環境の改善と組織の生産性向上のために重要な取り組みである5Sですが、実際にどのように進めるべきか悩んでいる方も多いのではないでしょうか。
ここでは、5Sの各ステップについて具体的な実践方法を解説し、5S活動の定着と活性化のためのヒントを提供します。整理、整頓、清掃、清潔、躾の各要素と目的をしっかりと理解し、効果的に取り組みましょう。
◾️ 1.「整理」:整理のポイントと実践方法
整理とは、必要なものと不要なものを区別し、不必要なものを排除することです。最終的には「必要なものだけすっきりと残った状態」を目指しましょう。目的は従業員全員が現状把握をすることです。十分な作業スペースを確保し、物事に優先順位をつけることで職場環境も、頭の中もスッキリします。
【実施方法】
- 現場にある全ての物品をリストアップし、使用頻度や重要度を基準に分類する。
- 不要なものは即座に処分し、必要なものだけを残すようにする。
【ポイント】
- 現場にある全ての物品をリストアップし、使用頻度や重要度を基準に分類する。
- 不要なものは即座に処分し、必要なものだけを残すようにする。
◾️ 2.「整頓」:整頓のポイントと具体例

整理で必要なもの、やるべきことを把握したら、整頓をしましょう。整頓は、必要なものをすぐに取り出せるように配置することで、作業効率の改善を図ります。
例えば、使用頻度の高い工具や書類は、作業場所の近くに配置し、ラベルを付けて視覚的に分かりやすくします。これにより、探す時間を短縮し、作業効率を大幅に向上させることができます。
【ポイント】
- 物の配置は、誰が見てもすぐに分かるものにすること。
- 色分けや形状を利用した収納方法を取り入れること。
視覚的に整理された環境を作り出し、ミスやロスを防ぐことができます。
◾️ ★初心者でもすぐ出来る「定位置」を取り入れた整理整頓の工夫
初心者でもすぐに取り入れられる「定位置」管理は、整理整頓の基本です。定位置とは、物の置き場所を決めておくことで、必要なものをすぐに見つけられるようにする方法です。
工具や書類の定位置はラベルで明示し、使ったら必ず元の位置に戻すルールを作りましょう。 このシンプルな工夫が、時間の無駄を防ぎ、職場全体の効率向上につながります。
◾️ 3.「清掃」:清掃の効果~職場環境美化以外のメリットも!~

整理・整頓が終わったら、次は清掃です。ここでいう清掃とは、機械や設備の点検も含みます。
定期的な清掃により、機械の故障を未然に防ぎ、作業環境を整えることができます。定期的な清掃活動が、従業員の健康を守ることにつながります。
清掃は単なる美化活動ではなく、職場の安全性と効率を高める重要なステップであることが分かりますね。
【ポイント】
- 事前準備として、清掃箇所を明確にし、担当者・清掃時間を決めて定期的に実施できるよう、スケジュール化すること。
- 清掃を通じて職場の問題点を発見した場合は、すぐに共有し合える仕組みを作り、問題点に対する改善策を講じること。
◾️ 4.「清潔」:清掃と清潔の違い。清潔に保つ目的とは?
清掃が一時的な汚れの除去を指すのに対し、清潔はその状態を維持することを意味します。清潔を保つ目的は、常に快適で安全な職場環境を維持し、従業員の健康を守ることです。これにより、長期的な視点での生産性向上が期待できます。
【ポイント】
- 清掃後の状態を基準として、従業員全員がどのような状態であるべきかを認識すること
- 小さな汚れや乱れであっても、清掃(点検も含め)は徹底して行うこと
全員が「清潔である状態」を把握し、清潔さを保つためのルール・やり方を明確にすることが重要ですね。
◾️ 5.「躾」:習慣化するための最後のステップ!

躾は、5S活動を日常業務に組み込み、習慣化することを指します。これにより、5Sが単なる一時的な取り組みではなく、組織の文化として根付くことが可能になります。従業員一人ひとりが5Sの重要性を理解し、継続的に実践することが求められます。
【ポイント】
- 5S活動の実施・振り返りを定期的に活動すること
- 5S活動を定着させる教育係や、活動を推進するリーダー等の担当を事前に決めること
達成度を確認しながら、従業員全体を巻き込み、モチベーションを高く持ち取り組んでいくことが、5S活動を組織全体に浸透させるコツです。
工場での5Sの活用法・企業の成功事例

ここでは、実際の工場での5S活動の事例を交えながら、活用法を紹介します。自分の職場では取り組めそうな事例はあるか、どのように実施できるか、を是非イメージしてみてください。
◾️ 製造ラインでの「整理」の事例
製造ラインでの整理は、不要なものを排除し、必要なものだけを適切に配置することから始まります。
ある工場では、定期的に全スタッフが参加する整理イベントを開催し、使用頻度の低い工具や部品をリスト化し、保管場所を見直しました。この結果、作業スペースが広がり、作業者の動線が短縮され、作業効率が向上しました。
◾️ 整頓による作業効率の向上策
整頓は、必要なものをすぐに見つけられるように配置することが目的です。
ある工場では、工具や部品に色分けされたラベルを貼り、収納棚に番号を振ることで、誰でもすぐに目的のものを取り出せるようにしました。これにより作業者は、探す時間を大幅に削減でき、結果として生産性が向上しました。また、整頓のルールを全員で共有することで、職場全体の意識改革にもつながっています。
◾️ 清掃活動の定期化による安全性確保
清掃活動を定期化することで、職場の安全性を確保することができます。
ある製造現場では、毎週末に全員参加で清掃活動を行うことをルール化しました。この際、清掃チェックリストを使用し、特に危険箇所や汚れやすい場所を重点的に清掃しています。これにより、機器の故障リスクが減少し、作業環境が常に安全で清潔に保たれるようになりました。清掃の意識を高めることで、事故の未然防止にもつながっています。
◾️ 5Sの維持・習慣化(清潔・躾)の事例
5S活動の維持と習慣化は、清潔と躾の徹底によって達成されます。
ある企業では、5S活動報告会を定期開催し、優れた取り組みを表彰する制度を導入しました。このように、成果を共有し、称賛することで、従業員のモチベーションを高めています。また、日常的に5Sの重要性を教育し、新入社員にも徹底することで、全員が自然と5Sを意識する文化が醸成されました。これにより、5S活動が職場の習慣として定着しています。
◾️ 大手製造業の5S導入による生産性向上事例

トヨタ自動車は、5S活動を通じて生産性の向上を実現した代表的な企業です。トヨタでは、整理整頓を徹底し、部品や工具の配置を最適化することで、作業効率を大幅に向上させました。これにより、製造ラインの停滞が減少し、納期遵守率の向上にもつながりました。さらに、定期的な清掃活動を通じて、職場の安全性を確保し、従業員の意識改革を促進しました。このような取り組みは、他の製造業にも応用可能であり、5Sの効果を最大限に引き出すための良い手本となっています。
◾️ 中小企業におけるコスト削減成功事例
中小企業の株式会社山田製作所は、5S活動を通じてコスト削減に成功しました。特に、整理と整頓を徹底することで、材料や部品の無駄を削減し、在庫管理の効率化を図りました。これにより、不要な在庫の削減と購買コストの削減を実現しました。また、清掃と清潔の維持により、設備の故障を未然に防ぐことができ、修理費用の削減にもつながっています。5S活動を通じたコスト削減は、特に資金に限りのある中小企業にとって、大きなメリットとなるでしょう。
(株式会社山田製作所 | 働き方改革特設サイト | 厚生労働省)
◾️ 5Sを活用した安全意識の向上
5S活動を通じて安全意識の向上に成功した企業をご紹介します。日立化成(株) 山崎事業所では、安全ポイントの見える化を図り、従業員の安全意識が高まり、事故の発生防止につなげています。また、整理(備品棚、資材置き場)や躾(無災害継続記録)の見える化等、5Sの各要素を従業員全員で常態把握ができるのは素晴らしく、私たちもすぐに見習いたいですね。
5S3定活動推進による危険源の『見える化』 – あんぜんプロジェクト
「5Sが製造業をダメにした」って本当?誤解される理由と正しい理解
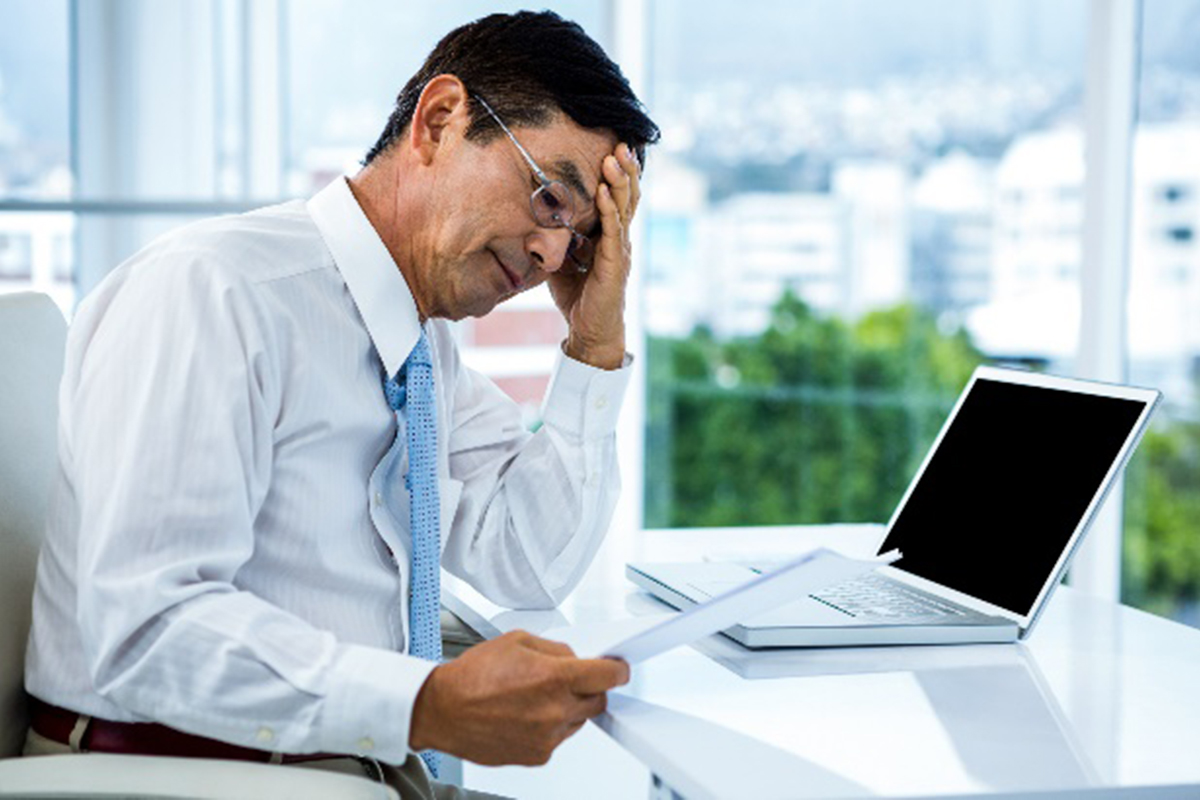
5S活動は製造業において重要な役割を果たしているにもかかわらず、「5Sが製造業をダメにした」といった批判を耳にすることがあります。
この見出しでは、5Sに対する誤解がなぜ生じるのか、そしてそれを正しく理解するためのポイントを探ります。5Sの本来の目的やその効果を再確認し、製造業の改善にどう役立つのかを詳しく解説します。
◾️ 5Sが失敗・形骸化してしまう理由とその対策
5S活動が失敗に終わる要因として、形骸化が挙げられます。
形骸化とは、形式だけが残り、実質的な効果が失われることです。5Sの目的や意義が現場で十分に理解されていないことで形骸化が引き起こされます。
特に、上層部からの指示だけで進められると、現場のスタッフが主体的に取り組む意欲を失ってしまいます。
もう一つの5S活動の失敗の要因として、理解不足が挙げられます。
従業員の理解を得られない状態という意味ではなく、不十分なトレーニングやサポートの欠如により、理解されていない状態、周知不足という意味です。
5S活動を効果的に実施するためには、5S導入時に従業員がその目的や手法をしっかりと理解し、実践できるような環境が必要です。管理者や活動の推進者は、なぜ5Sが重要なのか、具体的にはどのような手順を踏むのか等綿密に計画を立て、従業員が疑問を抱いた際に適切に対応できるようにしましょう。
従業員全員が5Sの意義を理解し、日常業務に組み込むためには、定期的な教育やワークショップを通じて、5Sの目的を再確認する機会を設けると効果的です。
また、5S活動アイデアを現場から募ることで、スタッフの意識を高め、継続的な改善を促進します。
◾️ 「5Sが製造業をダメにした」と言われないための成功ポイント
5Sが製造業をダメにしたと評価されないためには、成功のためのポイントを押さえることが必要です。
まず、5Sの導入にあたり、全員参加の意識を高めることが重要です。これには、従業員が自らの改善アイデアを提案できる環境を整えることが含まれます。
さらに、5S活動を単なる整理整頓の取り組みと捉えず、職場の効率化や安全性向上に結びつける視点が求められます。
また、5S活動事例を他の工場やサービス業からも学び、成功事例を参考にすることも有効です。トヨタのように、5Sを企業文化として根付かせることで、持続可能な改善が可能になります。
5Sの目的を再確認し、ムリ・ムラ・ムダを排除する取り組みを続けることで、製造業における5Sの価値を最大限に引き出すことができるでしょう。
企業が直面する5S導入の課題と解決策

5S活動は職場環境の改善や生産性向上に貢献する重要な手法ですが、従業員の意識改革にも及ぶ抜本的な改善手法です。そのため、5Sを社内に広めて定着するのには課題を感じる担当者も多いです。
◾️ 5S活動の活性化のためにはどうすればいい?
- 定期的な5S活動の成果発表会開催をおすすめします。部署別に取り組みを共有するのもおすすめです。5S活動を通じて社内コミュニケーションが活発になり、社員全体のモチベーションを維持することができます。
- 活動の進捗を可視化するために、5Sチェックリストや進捗ボードを活用することも効果的です。どのプロセスが改善されているのか、どの部分に課題があるのかを明確に把握することができ、迅速な対応が可能になります。成功事例として、ある製造業の企業では、毎月の5S評価を行い、優秀なチームを表彰することで、活動の定着を促進しました。
◾️ 従業員の意識改革が起きるまで、5S活動のモチベーション維持に課題を感じていますが、解決策はありますか?
- 従業員が活動の意義を理解し、自発的に取り組むためには、教育とコミュニケーションが欠かせません。例えば、5Sの基本理念や成功事例を学ぶワークショップを定期的に開催し、従業員の理解を深めることが効果的です。
5S定着の第1歩に、「設備点検のDX」を取り入れるのはいかがでしょうか。
持続可能な5S文化を構築するためには、組織全体での一貫した取り組みが求められます。5S活動を一時的なプロジェクトとしてではなく、日常業務の一部として定着させることが重要です。持続的な活動の定着のためには、社員教育や社内コミュニケーションのほかに、現場主体のDX推進をしていくことをおすすめしています。
株式会社AIoTクラウドでは、企業の設備保全・点検業務を効率化するソリューション、設備点検DXサービス『WIZIoT(ウィジオ) 』を提供しています。
工場設備のメーターなどを固定カメラやスマホカメラで撮影、AIが読み取り、クラウド上の点検台帳に自動的に記録することで、点検業務の時間短縮、ヒューマンエラーの低減を実現するSaaS型サービスです。
5Sの要素「清掃」で欠かせない点検業務ですが、現場主体点検業務が定着し、データの可視化もできることから、お手軽に現場主体のDX推進が可能です。
持続的な企業の成長を実現するために、ぜひ現場で始めるDXの第1歩として、点検業務を見直してみませんか?
設備点検DXサービス『WIZIoT(ウィジオ)』
サービスの資料ダウンロードはこちら
設備点検DXサービス『WIZIoT(ウィジオ)』
サービスへのお問い合わせはこちら
設備点検DXサービス『WIZIoT(ウィジオ)』
サービスの無料トライアルはこちら