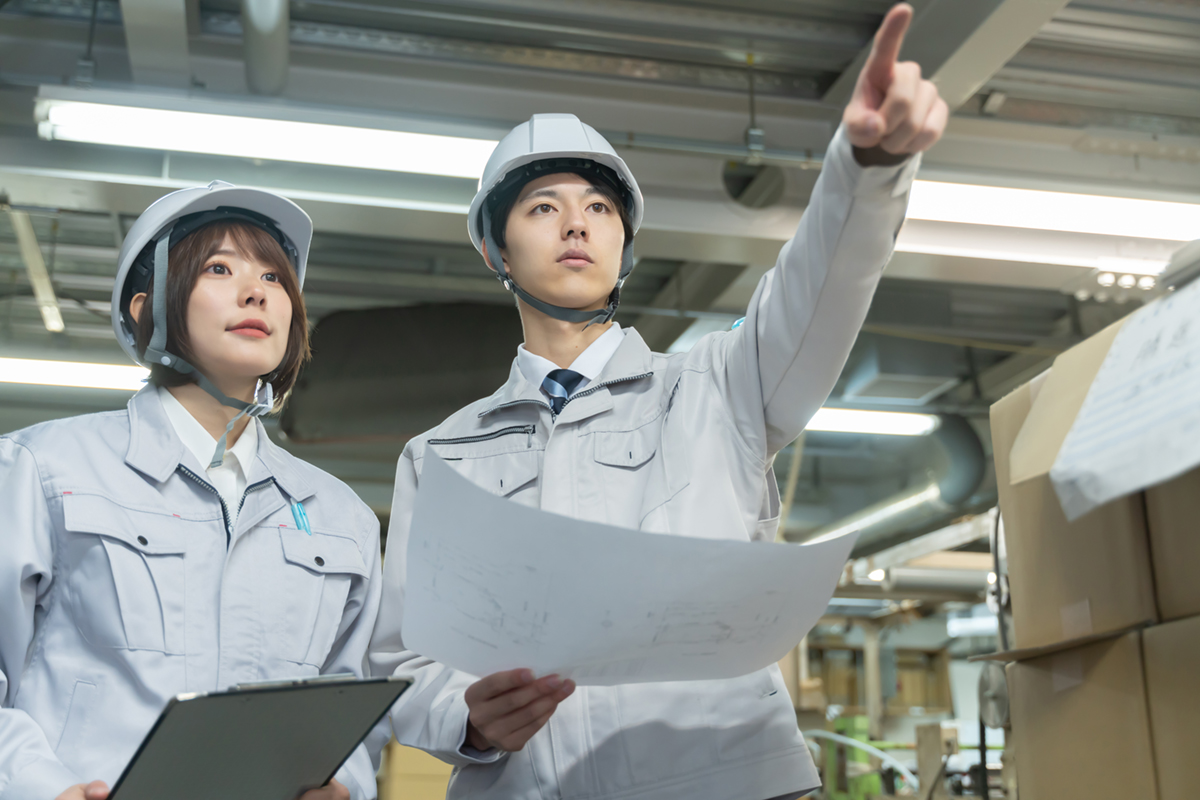
予防保全は、製造現場での故障やトラブルを未然に防ぐための重要な保全方法です。予防保全にはさまざまな方法がありますが、本記事では予防保全の基礎知識や、そのほかの方法との違いを徹底解説します。メリットやデメリット、導入のためにすべきことなどをご紹介するので、導入を検討している方はぜひお役立てください。
2025/02/17 公開
予防保全とは?
予防保全(PM:Preventive Maintenance)とは、設備や機械の故障やトラブルを未然に防ぐために、定期的に点検・メンテナンスを行う保全方法のことです。故障やトラブルの発生を防ぐために事前に問題を特定し適切な対策を講じることで、設備の安定稼働を維持することを目的としています。
設備のトラブルや劣化を早期に発見して、点検や部品の交換などの適切な対策を講じれば、予期せぬダウンタイムや生産効率の低下を防げます。
他の保全方法との違い
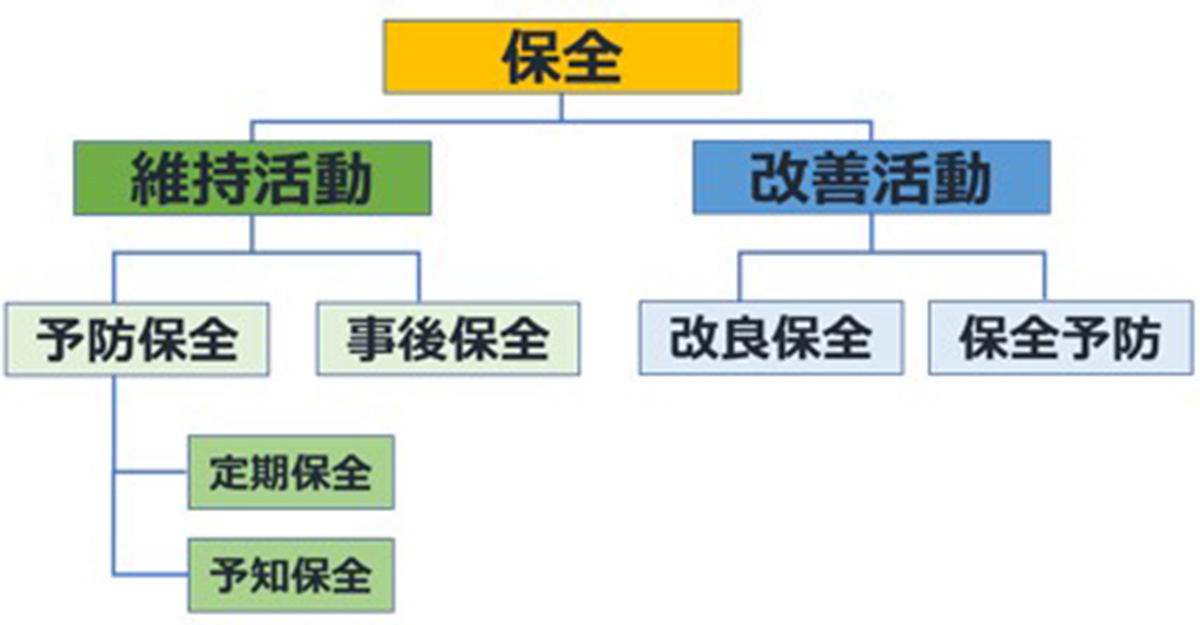
予防保全以外にも、保全の方法はさまざまなものがあります。以下で、予防保全とそれぞれの保全方法との違いを詳しく見ていきましょう。
◾️ 予防保全と事後保全の違い
事後保全(BM:Breakdown Maintenance /※RM:Reactive Maintenanceとも呼ばれる)は、設備の故障が発生してから対処を行なう保全方法です。
予防保全と事後保全の違いは「保全のタイミング」にあります。予防保全は故障が発生する前にメンテナンスを行うのに対して、事後保全は故障が発生した後に対処をします。
事後保全は故障やトラブルが発生してから対処するため、突発的なトラブルに対して迅速に対応しなければなりません。トラブルを未然に防止する予防保全とは、真逆の保全方法といえるでしょう。
◾️ 予防保全と定期保全の違い
定期保全(TBM:Time Based Maintenance)は、設備の故障を防ぐために、あらかじめ決められたスケジュールに従ってメンテナンスを実施する方法です。
故障やトラブルの有無に関わらず、時間や使用期間に基づいて定期的に点検や部品の交換を行います。トラブルを未然に防ぐという意味で、定期保全は予防保全の一種といえます。
◾️ 予防保全と予知保全の違い
予知保全(PM:Preventive Maintenance)は、センサーやIoT技術を活用して、リアルタイムで機械の状態を監視し異常を検知することで、故障の兆候を早期に察知する保全方法です。
工場内の機械・設備の状態を監視し、その状態に応じてメンテナンスを実施する保全方式で、状態基準保全(CBM:Contition Based Maintenance)という意味があります。定期保全とは異なり、メンテナンスのスケジュールを決めることはありません。
IoTやAI技術を駆使して機械の動作パターンを解析すれば、通常とは異なる動きも特定できます。予防保全と比較してより高度で精密な技術が求められるため、導入には一定のコストがかかりますが、その分だけ得られる効果も大きいです。
◾️ 予防保全と予兆保全の違い
予兆保全は、設備や機器が壊れそうな予兆を捉えた段階で保全を行う方法です。異常が発見されてから点検をするのではなく、その前の段階で保全が行うため、異常の早期発見と対応が可能になります。予兆保全と予知保全とほぼ同じ意味です。
◾️ 予防保全と改良保全の違い
改良保全(CM:Corrective Maintenance)とは、設備が故障した際に、同じ問題が再発しないように、既存の設備を改良して、性能を向上させる保全方法です。故障や異常を検知するための保全ではなく、故障原因を根本的に改善するのが目的といえます。
コストはかかりますが、設備の故障による損害の方が大きい場合には、導入が検討されます。
◾️ 予防保全と保全予防の違い
保全予防(MP:Maintenance Prevention)は、保全を予防するために設備導入の計画段階で、操業開始後の故障や不良の発生を予測し、故障の原因となり得る要素を排除して、耐用年数をより長くしたり、メンテナンスしやすいように設計したりする保全方法です。
予防保全(PM:Preventive Maintenance)とは、言葉の順番を変えただけではなく、意味が全く違います。
設備の導入時点で行うより根本的なアプローチでもあり、設備の初期投資は増加しますが、長期的にはメンテナンスコストの削減や信頼性の向上につながります。
予防保全の種類
予防保全の種類は、主に上記の4つに分類されます。では、1つずつ詳しく見ていきましょう。
◾️ 時間基準保全 (TBM)
時間基準保全(TBM:Time Based Maintenance)は、一定の時間間隔で設備や部品のメンテナンスを行う手法です。設定した周期を基準として計画的に部品を交換することで、設備の安定稼働を確保します。
TBMの実施するときは、設備の故障履歴やメーカーの推奨メンテナンス周期などの客観的なデータを参考にしながら、最適なタイミングを見極めるのが重要です。
◾️ 利用基準保全 (UBM)
利用基準保全(UBM:Usage Based Maintenance)は、設備の使用状況を基準にメンテナンスを行う手法です。稼働時間や利用量などの利用実績をもとに、適切な保全計画を策定します。
時間ではなく稼働状況に基づいて保全を行うため、設備の使用頻度が変動する場合や、特定の使用条件下での劣化が懸念される場合に有効です。
UBMの利点は、実際の使用状況に応じた柔軟なメンテナンスが可能な点にあります。設備の使用データを正確に収集・分析し、最適な保全スケジュールを策定することが求められます。
◾️ 状態基準保全 (CBM)
状態基準保全(CBM:Condition Based Maintenance)は、設備の実際の状態を測定し、不具合や劣化の兆候が見られた場合に交換や修理を行う手法です。
利用環境によって同じ稼働時間や利用量でも劣化具合が異なるため、実際の状態を基準にすることも重要です。設備の状態に基づくため、必要な保全を的確に行うことができます。
◾️ 故障発見保全 (FFM))
故障発見保全(FFM:Failure Finding Maintenance)は、設備の隠れた故障を発見し、大規模なダウンタイムを防ぐ手法です。普段は稼働していないが、故障して正常に動作しないと重大な影響を及ぼす可能性のある設備に使われます。主に漏電ブレーカやスプリンクラーなどの予防に有効です。
その他、配管や配線など動作を伴わない静的な設備に関してもFFMが用いられます。
予防保全のメリット
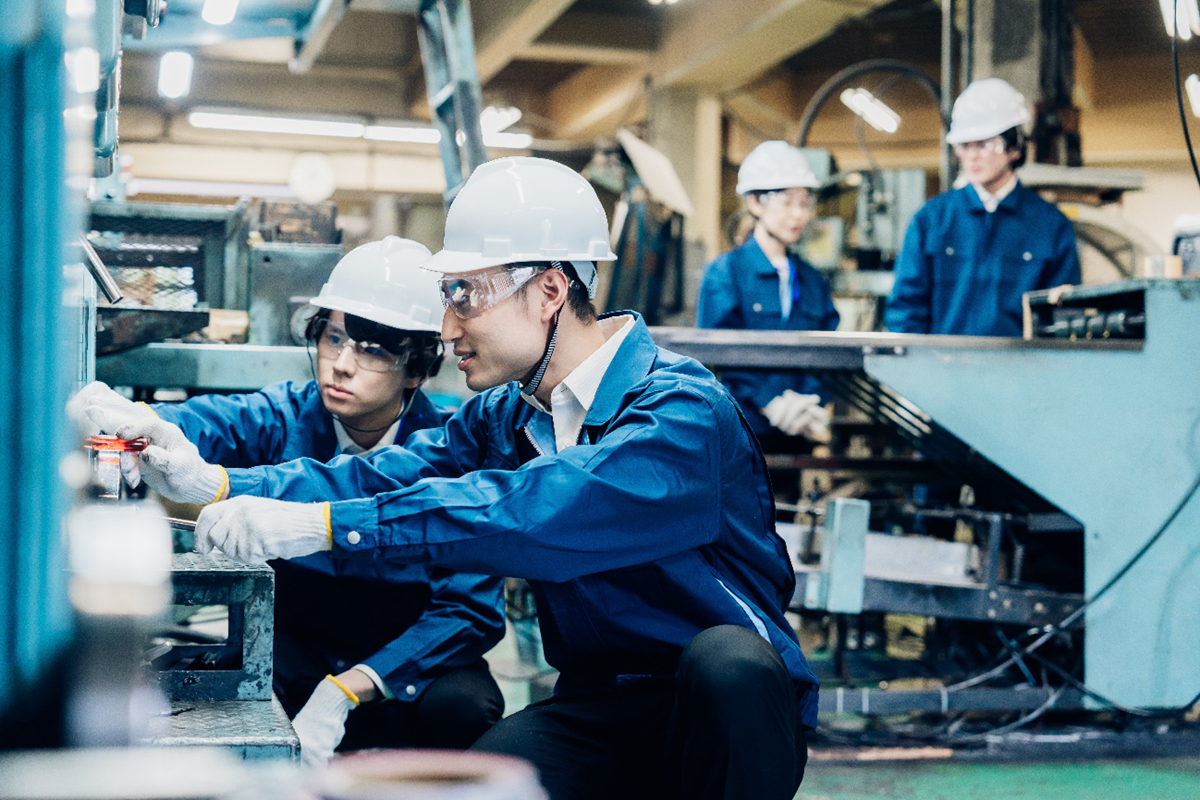
予防保全のメリットは、主に上記の4点が挙げられます。1つずつ詳しく見ていきましょう。
◾️ 製品の品質を維持できる
予防保全を行うことで設備や機器の劣化や不具合がない状態で稼働させられるため、品質基準を満たす製品を安定して生産できます。また、設備の状態を常に良好に保てば、製品のバラつきも減少させられます。
製品の品質低下を未然に防ぐことで顧客満足度も向上し、品質トラブルによる損失も防げるでしょう。
◾️ ダウンタイムを回避できる
設備や機器に故障が発生すると、トラブル解消までのダウンタイムが生じます。状況によってはダウンタイムが長期に渡る可能性があるため、故障する前のメンテナンスが重要です。
予防保全を行えば、予期せぬ停止を防ぎ生産ラインの中断を最小限に抑えられます。これによりダウンタイムの発生を抑え、生産性の向上やコスト削減も実現できるでしょう。
◾️ 部品の過剰在庫を防げる
予防保全を適切に実施することで、修理やメンテナンスで必要な部品の過剰在庫を防げます。設備の状態を正確に把握し、必要な部品を適切なタイミングで交換できるため、不要な在庫を削減できます。これにより、在庫管理コストも削減できるでしょう。
劣化の具合も事前に把握できるようになれば、必要な部品の購入契約も立てやすくなります。
◾️ 保全担当者の働き方が改善できる
予防保全を導入することで、保全担当者の働き方を大幅に改善できます。予防保全は事後保全に比べて計画的に作業が進められるため、突発的なトラブルが発生する可能性が低くなり、緊急対応の頻度も減少します。
緊急対応が減少すれば、休日や夜間の勤務時間外の呼び出しによる担当者の業務負担も軽減されるでしょう。労働環境が改善されれば、長期的な人材の確保にもつながります。
予防保全のデメリット
予防保全にはいくつかのデメリットも存在します。たとえば、予防保全を導入すると故障の有無にかかわらず工数が発生するため、より多くのリソースが必要です。さらに、定期的なメンテナンスが必要なため、全体の作業工数が増えます。
実際には故障しない部品や設備に対しても、過剰なメンテナンスを行うリスクがあるため、費用対効果が低い可能性もあるでしょう。また、計画的なメンテナンスを行うためのスケジュール調整にも労力を割かなければなりません。
予防保全の実現に向けてすべきこと
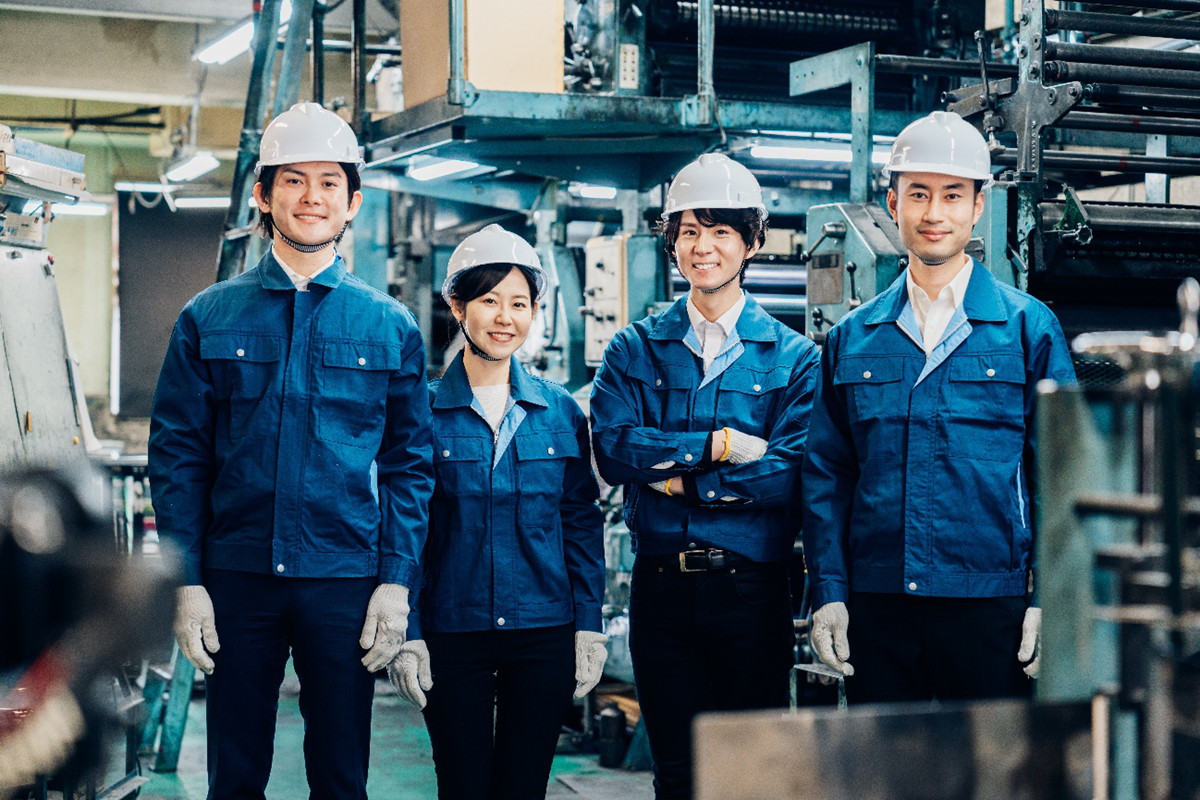
予防保全を導入するために重要なポイントを解説します。以下3点を押さえ、効果的な予防保全の実現を目指しましょう。
◾️ 保全計画を策定する
予防保全を導入するうえでまず重要なのは、詳細な保全計画の策定です。計画を策定する段階で、設備の特性や使用状況に基づき、適切な保全基準や実施手順を明確に定めてください。メーカーが提示する使用回数や期間だけでなく、現場の保全担当者の経験の両方を考慮することが重要です。
また、点検周期や点検内容もあらかじめ決めておきましょう。さらに、保全計画は定期的に見直し、設備や環境の変化に対応できるようにしてください。
◾️ 実施手順をマニュアル化する
保全作業の抜け漏れを防ぐためには、実施手順をマニュアル化し全員が同じ基準で作業を進められることが大切です。マニュアル化によって保全担当者が一貫した方法で作業できるため、効率性の向上とミスの削減にもつながります。
マニュアル作成では、文字だけでなく写真なども活用して分かりやすさを重視し、作業の注意事項がある場合に備えて備考欄を設けておきましょう。
◾️ 保全記録を管理する
保全記録を管理することで設備の状態を正確に把握し、適切な保全活動を行うことが可能になります。記録を正確に残せば、設備の故障傾向を分析でき、より効果的な予防保全ができるでしょう。
また、データを一元管理し記録管理を徹底することで、過去の保全履歴に基づいた改善案の提案や、次回の保全計画の策定などもスムーズに進められます。
保全データを管理するには、設備点検DXサービス『WIZIoT(ウィジオ) 』がおすすめです。設備点検DXサービス『WIZIoT(ウィジオ) 』は、工場や製造業向けに開発されたIoTサービスです。スマホカメラによる読み取りや固定カメラによる撮影でメーターの数値を読み取れるため、保全業務を従来よりも短時間で効率的に行えます。
読み取ったデータはクラウド上に記録され、一元的に管理できるため、情報の共有や分析も可能です。効率的かつ精度の高い点検が行えるため、設備や機器の故障も未然に防ぎ、異常の早期発見にもつながります。スマホアプリと固定カメラの2つのタイプをご用意しており、とくにスマホアプリ・カメラは、リーズナブルかつ簡単に導入できるため、工場のDX化を進める第一歩としておすすめです。
サービス利用イメージ

『WIZIoT(ウィジオ)』スマホアプリの3つの特長!
-
スマホをメーターにかざすだけのスピーディー連続自動撮影で、点検時間を約80%削減
スマホをメーターの上にかざすだけで素早く連続的に自動撮影をおこない、点検時間を約80%短縮します。 -
異音・異臭等の設備点検も記録できる!
異音・異臭など計器以外の設備点検記録も、スマホアプリ1つで簡潔します。 -
紙の帳票は、もう要らない!
点検記録の報告から承認まで、まとめてデジタル化。Web上の点検台帳で数値や画像をいつでも確認でき、異常値の場合もメール通知で素早い対処が可能です。
『WIZIoT(ウィジオ)』固定カメラの特長!
-
固定カメラによる自動撮影・AI読み取りで巡回いらず!
メーターを固定カメラで読み取れば、AIが自動点検を実施。リモートでの巡回点検が可能なほか、高所や暗所などの危険な点検作業も回避できます。
設備点検DXサービス『WIZIoT(ウィジオ)』
サービスへのお問い合わせはこちら
設備点検DXサービス『WIZIoT(ウィジオ)』
サービスの資料ダウンロードはこちら
設備点検DXサービス『WIZIoT(ウィジオ)』
サービスの無料トライアルはこちら
予防保全でトラブルを未然に防止しよう!
予防保全を行えば、設備や機器の故障を未然に防ぎ、生産活動の効率性維持や品質の安定につながります。重大な事故や設備の停止などのリスクにも備えられるため、顧客満足度のだけでなく、従業員の安全性向上にもつながるでしょう。
製造現場の安定稼働や品質維持、労働環境の向上など、さまざまなメリットが得られるため、課題解決のために予防保全の導入をおすすめします。
予防保全の導入をお考えの方は、設備点検DXサービス『WIZIoT(ウィジオ) 』の導入をぜひご検討ください。スマホカメラや固定カメラを用いたメーターの自動読み取りと、クラウド上でのデータ一元管理で、業務の効率化を実現します。
作業時間の短縮や業務負担の軽減、データ管理の正確性など、保全業務の生産性の向上に役立ちます。現場での保全業務に課題を抱えている方は、お気軽にお問い合わせください。
設備点検DXサービス『WIZIoT(ウィジオ)』
サービスへのお問い合わせはこちら
設備点検DXサービス『WIZIoT(ウィジオ)』
サービスの資料ダウンロードはこちら
設備点検DXサービス『WIZIoT(ウィジオ)』
サービスの無料トライアルはこちら